Ace Info About What Is The Detailed Bill Of Materials
![Free Printable Bill Of Material Form Templates [PDF, Excel] Free Printable Bill Of Material Form Templates [PDF, Excel]](https://www.typecalendar.com/wp-content/uploads/2023/05/Bill-of-Material-1-1024x576.jpg)
Free Printable Bill Of Material Form Templates [PDF, Excel]
Unlocking the Secrets of a Detailed Bill of Materials (BOM)
1. What exactly are we talking about?
Ever wondered how complex products come together? Think about your smartphone, your car, or even that fancy coffee maker. They aren't just magically assembled. Behind each of them lies a crucial document: the Bill of Materials, or BOM. And when we say "detailed bill of materials," we're talking about a BOM on steroids! It's not just a list; it's a comprehensive, granular breakdown of everything needed to manufacture a product.
Imagine trying to bake a cake without a recipe. You might end up with something vaguely edible, but it probably won't be the masterpiece you envisioned. A detailed BOM is like that recipe, but instead of sugar and flour, it's got every single component, raw material, sub-assembly, and even the adhesives required to put it all together. It's the blueprint for bringing a product to life.
So, why is "detailed bill of materials" the keyword we're focusing on? Because simply having a BOM isn't enough. The level of detail within the BOM directly impacts efficiency, cost control, and overall product quality. A vague BOM can lead to errors, delays, and a whole lot of frustration. A detailed BOM, on the other hand, empowers manufacturers to streamline their processes and minimize potential problems.
In essence, the "detailed bill of materials" is more than just a list; it's a strategic tool. It's a communication hub for engineering, procurement, manufacturing, and even finance. It ensures everyone is on the same page, working with the same information, and striving toward the same goal: creating a high-quality product, efficiently and cost-effectively.
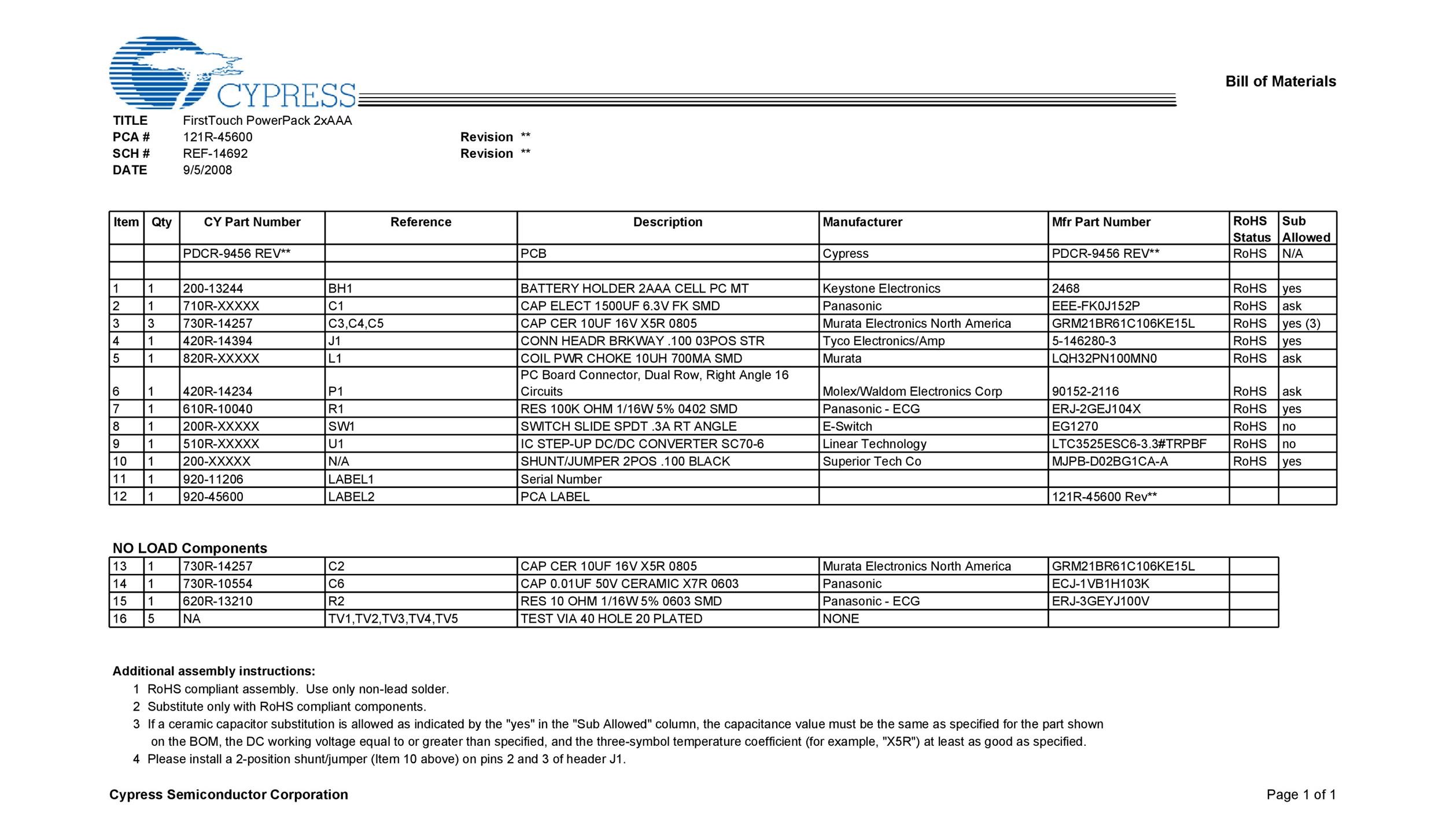
Bill Of Materials Template
Why Detail Matters
2. The ripple effect of accurate information.
Think of a detailed BOM as the foundation upon which a successful product launch is built. Without it, you're essentially building a house on sand. One of the biggest advantages is improved accuracy in ordering and inventory management. With a detailed BOM, you know exactly what you need, how much you need, and when you need it. This minimizes the risk of stockouts (which can halt production) and overstocking (which ties up valuable capital).
Cost control is another major benefit. A detailed BOM allows you to accurately calculate the cost of each component and sub-assembly. This makes it easier to identify potential cost-saving opportunities, negotiate better prices with suppliers, and track expenses throughout the manufacturing process. Imagine being able to pinpoint exactly where your costs are coming from — it's like having X-ray vision for your budget!
Furthermore, a comprehensive BOM streamlines the manufacturing process itself. With clear instructions and precise specifications for each step, workers can assemble products more efficiently and accurately. This reduces the likelihood of errors, rework, and delays. It's like giving your assembly line a supercharge of clarity and precision.
But the benefits don't stop there. A detailed BOM also improves product quality. By specifying the exact materials and processes to be used, you can ensure that each product meets the required standards. This reduces the risk of defects and improves customer satisfaction. Happy customers mean repeat business and a stronger brand reputation — which is always a good thing!
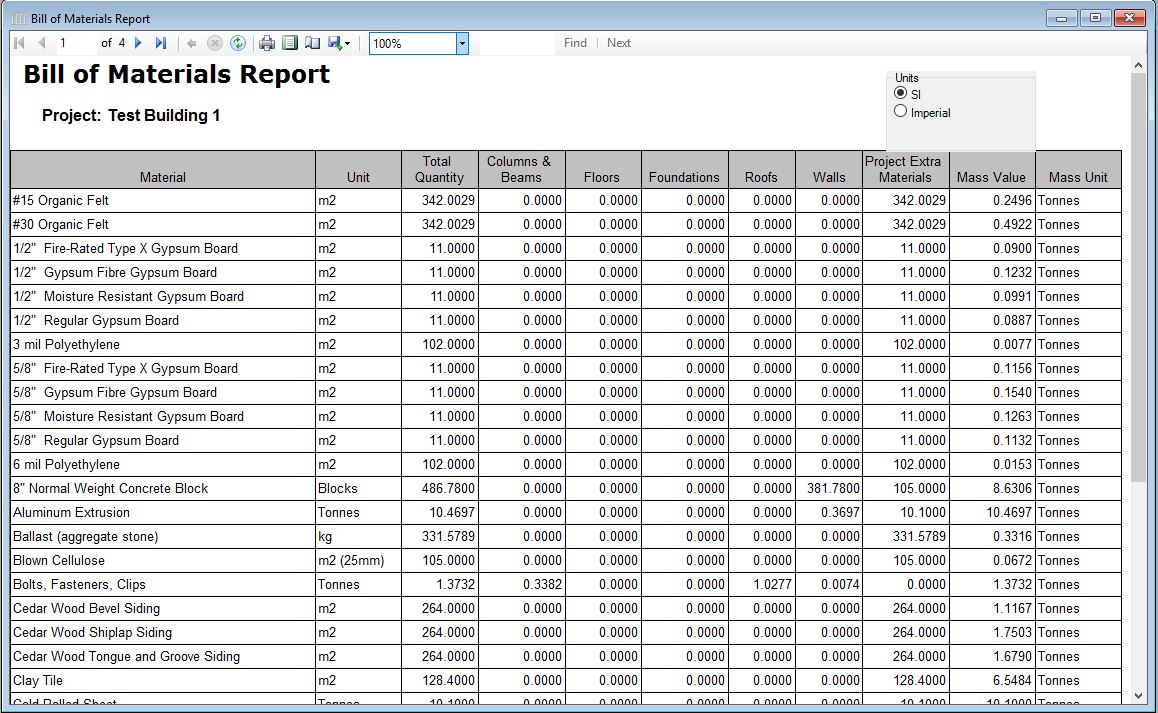
Bill Of Materials Lasopabrothers
Navigating the Elements
3. Dissecting the Anatomy of the BOM
Okay, so we've established that a detailed BOM is important. But what exactly goes into one? What are the essential elements that make it so comprehensive? First and foremost, you need a complete list of all parts and materials. This includes everything from the obvious components to the seemingly insignificant items like screws, washers, and labels. Don't leave anything out!
Each part should be identified with a unique part number or identifier. This makes it easier to track components throughout the manufacturing process. Think of it as giving each part its own social security number. Along with the part number, you'll need a detailed description of each part. This should include specifications such as size, material, and finish. The more detail, the better!
The BOM should also specify the quantity of each part required to manufacture one unit of the finished product. This is critical for accurate ordering and inventory management. It's not enough to know that you need screws; you need to know exactly how many screws you need. Furthermore, the BOM should indicate the unit of measure for each part. Is it measured in pieces, feet, or kilograms? Clarity is key.
Finally, a detailed BOM will often include information about suppliers, costs, and lead times. This allows you to easily track down the parts you need, compare prices, and plan your production schedule accordingly. Think of it as having a Rolodex of suppliers right at your fingertips. By including all of these elements, you can create a BOM that is truly comprehensive and useful.

Bill Of Materials Or Bills Material Notebase
Beyond the Basics
4. Not all BOMs are created equal.
You might be surprised to learn that there isn't just one type of BOM. Different industries and manufacturing processes often require different approaches. Let's take a look at some of the most common types of BOMs. One popular type is the Engineering BOM (EBOM). This is created by the engineering team during the design phase and focuses on the functional aspects of the product.
Then there's the Manufacturing BOM (MBOM), which is used by the manufacturing team to build the product. The MBOM typically includes more detailed information about manufacturing processes and tooling. Think of the EBOM as the architect's blueprint and the MBOM as the construction crew's instructions.
Another type is the Sales BOM (SBOM), which is used to define a product as it's sold to customers. This might include options, configurations, and accessories. For example, a computer manufacturer might use an SBOM to define the different configurations of its laptops. And let's not forget the Configurable BOM (CBOM), which allows you to create different versions of a product from a single BOM. This is particularly useful for products that can be customized or configured in various ways.
Choosing the right type of BOM depends on your specific needs and manufacturing processes. Consider the complexity of your product, the level of customization you offer, and the specific requirements of your engineering, manufacturing, and sales teams. The important thing is to choose a BOM structure that provides the level of detail and flexibility you need to effectively manage your product lifecycle.
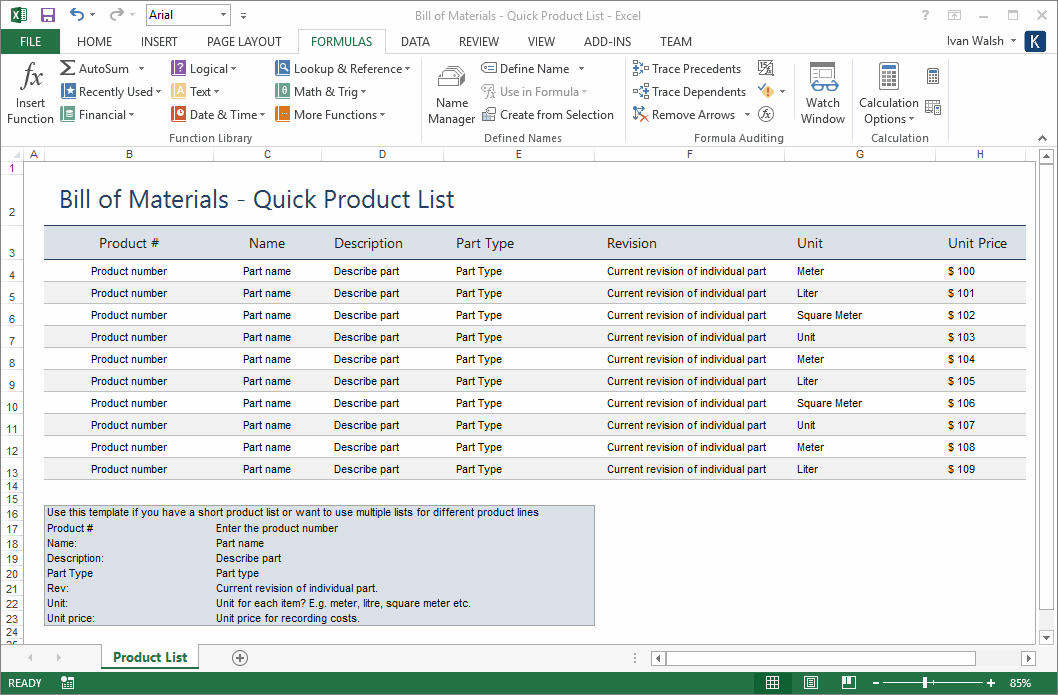
Bill Of Materials (BOM) Template Technical Writing Tools
Best Practices
5. Tips and tricks for BOM brilliance.
Creating a detailed BOM is one thing, but optimizing it for maximum efficiency is another. So, what are some best practices for making your BOM a lean, mean, manufacturing machine? First, strive for accuracy. Double-check all part numbers, descriptions, and quantities to ensure they are correct. Even a small error can lead to big problems down the line. It is better to take your time and make sure it is right the first time.
Second, use a consistent format. This makes it easier for everyone to understand and use the BOM. Consider using a standardized template or software program to ensure consistency. Make sure all team members are clear about the specific format you are using. Regularly review and update your BOMs to reflect any changes in design, materials, or manufacturing processes. A BOM that is out-of-date is worse than no BOM at all.
Another great practice is to integrate your BOM with other business systems, such as your ERP or MRP system. This allows you to automate many of the tasks associated with BOM management, such as ordering, inventory control, and cost accounting. This can significantly improve efficiency and reduce the risk of errors. By connecting your BOM to your other business systems, you can create a seamless flow of information throughout your organization.
Finally, don't be afraid to seek help from experts. There are many consultants and software providers who specialize in BOM management. They can provide valuable guidance and support to help you optimize your BOM for success. Remember, a well-managed BOM is a powerful tool that can help you improve efficiency, reduce costs, and enhance product quality. So invest the time and effort needed to get it right.
![FREE 23+ Bill Of Materials (BOM) Templates [EXCEL, WORD] FREE 23+ Bill Of Materials (BOM) Templates [EXCEL, WORD]](https://www.dailylifedocs.com/wp-content/uploads/2022/03/BOM-Template-2578924-1024x782.jpg)
FAQs
6. Your burning BOM questions answered.
Still scratching your head about detailed BOMs? Let's tackle some common questions. Here are a few FAQs to clear up any remaining confusion.
7. Question 1
Answer: A parts list is simply a list of parts. A BOM, especially a detailed one, includes much more information, such as quantities, specifications, costs, and supplier information. Think of it as a parts list with a whole lot of context.
8. Question 2
Answer: There are many options available, ranging from simple spreadsheets to sophisticated ERP systems. Popular choices include Autodesk Fusion 360, Arena PLM, and SolidWorks PDM. The best option for you will depend on your specific needs and budget.
9. Question 3
Answer: Ideally, you should update your BOM whenever there are changes to the product design, materials, or manufacturing processes. Regular reviews are also a good idea, even if there haven't been any recent changes. Treat your BOM like a living document that needs to be kept up-to-date.